Hydraulic equipment service - Bosch Rexroth products in our company
Rexroth traces its origins back to the late 18th century. Since then, the company has undergone various transformations, not only expanding the range of its products, but also contributing to technological innovations in the field of motion control systems.
Since 2001, the brand has been taken over by Bosch, thereby strengthening its position in the field of hydraulic component production, thanks to achieving global reach.
Hydraulic systems in construction machinery play a key role in enabling the execution of basic tasks of working equipment, such as load transfer, control of arm movement in an excavator, or precise vehicle control.
It can never be overstated how important it is to properly care for the hydraulics in your machine.
This article will remind you of the basic rules of dealing with the titular system, the principles of its operation and the critical components whose proper functioning is essential for the machine to perform its role well on the construction site.
The easiest way to present these principles is on a specific example and that's why the name of the Rexroth company, or rather Bosch Rexroth, was introduced in the first paragraph of this text. At WIBAKO, we often deal with components from this manufacturer, repairing pumps or motors of this brand. The popularity of Rexroth pumps has led us to dedicate a dedicated website to them - WIBAKO Hydraulics.
Before we move on to specific cases, let's present how a hydraulic system works and which components make up its core.
Power hydraulics - what is it? Principle of operation and key elements
Everything is based on the scheme of drawing fluid from the tank and pumping it through the pump to valves and cylinders. The hydraulic pump is the core of the entire process. Its design can be based on the movement of pistons, gears or a rotor with blades.
That's why we divide them into piston, vane and gear types. The first type uses the movement of pistons generating pressure and fluid flow to cylinders, which enables the operation of a specific part of the machine.
The second type of pump pushes hydraulic oil through the work of two gears. The first one is driven, and the second one rotates as a result of the action of the teeth of the first one. The change in space between them causes fluid flow to the cylinders.
The last case takes its name from the rotor equipped with blades, which, by rotating, cause the fluid to be sucked in and pump it further into the system. More details about the types of pumps and their use can be read in one of our articles.
The next element is a hydraulic motor powered by fluid pumped by the pump, and its role is to convert fluid energy into mechanical energy, which is the source of drive for individual machine functions, driving or rotation. By controlling the flow of hydraulic fluid, the operator adjusts the speed and direction of the motor's movement.
Hydraulic distributor - the control center for the flow of hydraulic fluid
The hydraulic distributor primarily plays a control role for the entire hydraulic system. The driver, by controlling the valves, allows hydraulic fluid to individual machine elements enabling such operations as lifting weights or rotary movement.
Distributors can be controlled mechanically using a lever or through a coil or solenoid valve (electronically), but in machines they are usually controlled hydraulically.
The hydraulic cylinder's fluid intake, for example, allows the excavator arm to be operated. The cylinder is built from a cylinder. Inside the cylinders there is a piston, the fluid supply causes its movement, which translates into generating mechanical force.
In summary, the operation of the hydraulic system is the pump's intake of oil from the tank and pumping it through the appropriate valve setting to specific parts of the machine.
Hydraulic filters - the basis for trouble-free operation
An important issue is also the operation of hydraulic filters. Proper filtration of hydraulic elements is necessary for the whole to be able to perform work tasks without failure. Hydraulic filters are to provide protection against contamination of hydraulic fluid, such as solid particles, chemical contamination, or water.
Lack of proper filtration leads to faster wear of parts including pumps, valves, motors and cylinders. Neglecting filtration review can result in a serious failure, which will immobilize the machine for a long time. Regular filter replacement protects against such a possibility and extends the life of components.
Rexroth hydraulic pumps - examples of devices and their service
Bosch Rexroth is a whole range of power hydraulics components - cylinders, motors, pumps, valves. Decades of experience and new technological solutions are visible in the manufacturer's offer. The multitude of components requires continuous improvement in technical knowledge and manual skills of mechanics, which we strive to meet at WIBAKO.
Moving on to specific examples of Rexroth products that we most often have to work with, they are undoubtedly hydraulic pumps. In our workshop, we carry out repairs of piston and vane pumps, we do not repair gear pumps due to their low durability.
Damage caused by gears causes the aluminum housing to be grooved, the replacement of which is out of the question due to the lack of spare parts. The pump is only suitable for replacement with a new one.
The characteristic pumps that we deal with are those with model designations A4VG, A11VO, A8VO or A10VO. Of course, there are many other models of Rexroth units that have undergone repair in our workshop, but based on these four cases we can bring closer what it looks like "from the kitchen" and what can be read from these markings.
“Travel” pump A4VG
The A4VG pump is a unit designed for closed circuits, as indicated by the last two letters "VG". It is characterized primarily by its use in travel drives e.g. in loaders.
The difference between an open and a closed circuit can be reduced to the rule that in the former, oil is supplied to receivers (e.g. hydraulic motors) via a distributor, and in the latter case it goes directly to the engine, bypassing its intermediation.
In open systems, the fluid from the receiver, once it has done its work, returns to the tank. In closed ones, however, it is pumped between the pump and the engine and returns to the pump.
Each pump has specified pressure parameters, both a minimum and maximum value, and the pressure is generated by the device and measured in bars, i.e. the force that is exerted on a unit of area (kg/cm2). Here, Pascal's Law is used - the pressure exerted from the outside on a liquid is the same throughout its volume.
A11VO - "pumping heart" of many machines
Rexroth A11VO is a variable output device, mounted in open systems. The "VO" suffix is an indication of this. It may optionally have a built-in rotor. This pump appears in many types of machines and often handles the service of those vehicle elements that have been assigned a specific job, such as an excavator arm.
This type of pump has a wide range of applications thanks to many control options that can be adapted to the construction equipment you have.
A8VO - one device, many possibilities
This model designation can be summed up as a excavator model, as it is mainly in these machines that we will find this pump. It is a two-section device mounted in open systems.
A two-section pump is made up of two sets of pistons, cylinders, timing plates and the rest of the components responsible for proper operation. This gives the user great possibilities for use in hydrostatic systems.
For example, the pump can simultaneously pump oil to two hydraulic motors that service the travel system in an excavator.
A10VO - quiet, small and efficient pump
The last model designation mentioned in this text is A10VO. A pump with variable output and just like the previous one, designed for open circuits. It has versatile application in hydrostatic systems of construction machines.
It is characterized by a low noise level and small dimensions. Flow manipulation is done through a control disc. The pump provides high power in relation to its dimensions.
Repairs of Rexroth hydraulic pumps in the WIBAKO workshop
Over many years of work, we have carried out countless repairs of hydraulic pumps, in 2022 alone there were over 200 of them and they often concerned Rexroth units. Each case starts with a verification of the wear and tear of specific pump components and separating those that are suitable for regeneration from those unfit for further use. We carry out all technical work after a thorough analysis of the device's condition.
It happens that the entire effort of the workshop is reduced to replacing a small part and general conservation work, such as cleaning, grinding and running in the pump, but there are also complicated repairs, where a larger number of components have been worn out and designated for replacement.
At this point, we can recall a few details from two repairs of pumps belonging to the same model family A4VG. One of the devices came to us in poor condition indicating serious damage and indeed, after diagnosing the efficiency of individual elements, many of them were replaced with new ones. This list included:
- cylinder
- pistons
- separator with ball
- disc springs
- swash plate
- bushings
- slide bearings
- charge pump
- shaft and body
This is an ideal example that can serve as a warning never to underestimate even trivial symptoms of improper functioning of the hydraulic system. The second case, despite the lack of general efficiency, only required seal replacement and running in, and after these activities the unit returned to efficiency.
We always disassemble pumps and get to the heart of the problem, and the culmination of the process is a test on the dynamometer, where we make sure that the pump has been effectively repaired.
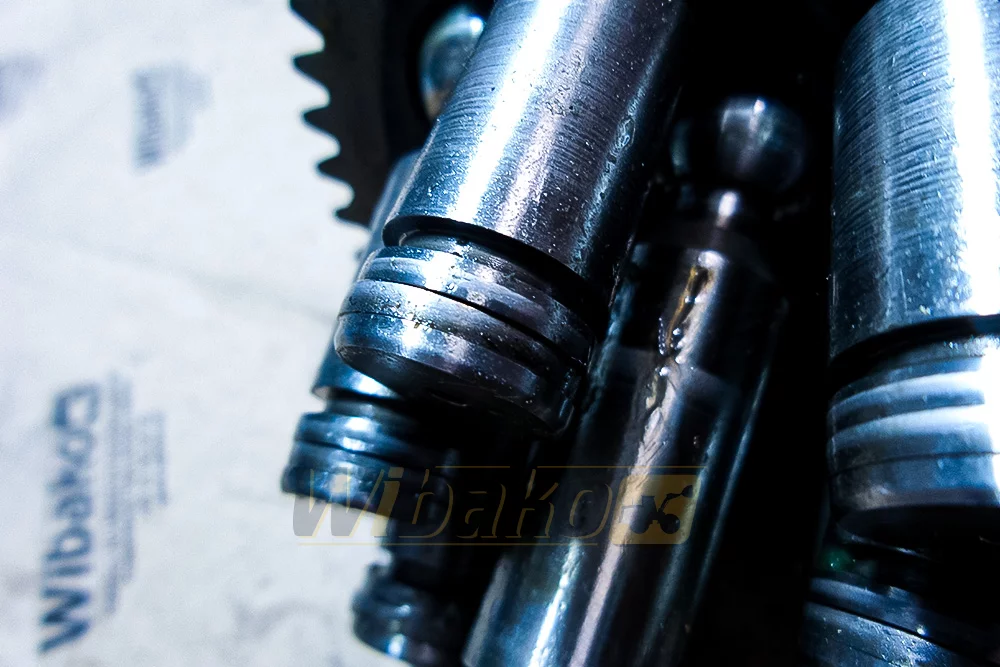